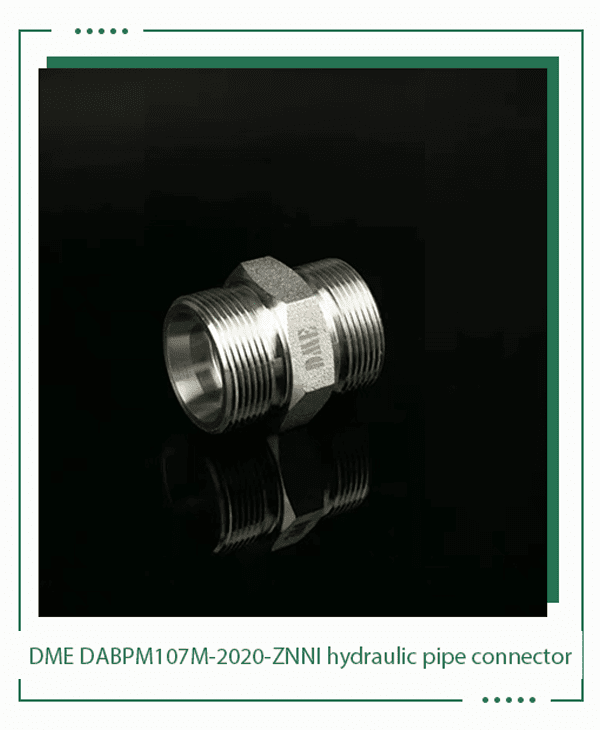
Corrosion is a key issue in extreme marine, mining, industrial and mobile applications, and many other markets, and can cause direct and indirect economic loss. In this regard, we have higher requirements for the corrosion resistance of hydraulic connector fittings.
Now, after more than 20 years of continuous exploration and development, DME machinery production equipment continuous iteration update, greatly improved the standard corrosion resistance of hydraulic fittings. The product has been upgraded from the original SAE standard of 72 hours for salt spray test to the standard of 400 hours within control, which is the baseline standard of our production.
However, we did not stop the pace of research and innovation. Recently, we have introduced zinc-nickel plating technology. Compared with SAEJ514 (ISO 9227 method) standard requirements, DME hydraulic fittings can remain up to 1,000 hours in salt spray test without red rust, and have remarkable corrosion resistance.
In order to prove the corrosion resistance of DME connector, we selected DME DABPM107M-2020-ZNNI hydraulic pipe connector, carried out salt spray test under ASTM B117 and ISO 9227 Standard Salt spray test condition, and recorded its change time.
Of course, DME hydraulic connectors not only have excellent corrosion resistance, but also retain torque value, friction coefficient, pressure grade, color and other key specifications that are important to customers to ensure a more stable hydraulic fluid transport carrier for hydraulic equipment and provide safe and effective connection solutions for your hydraulic system.